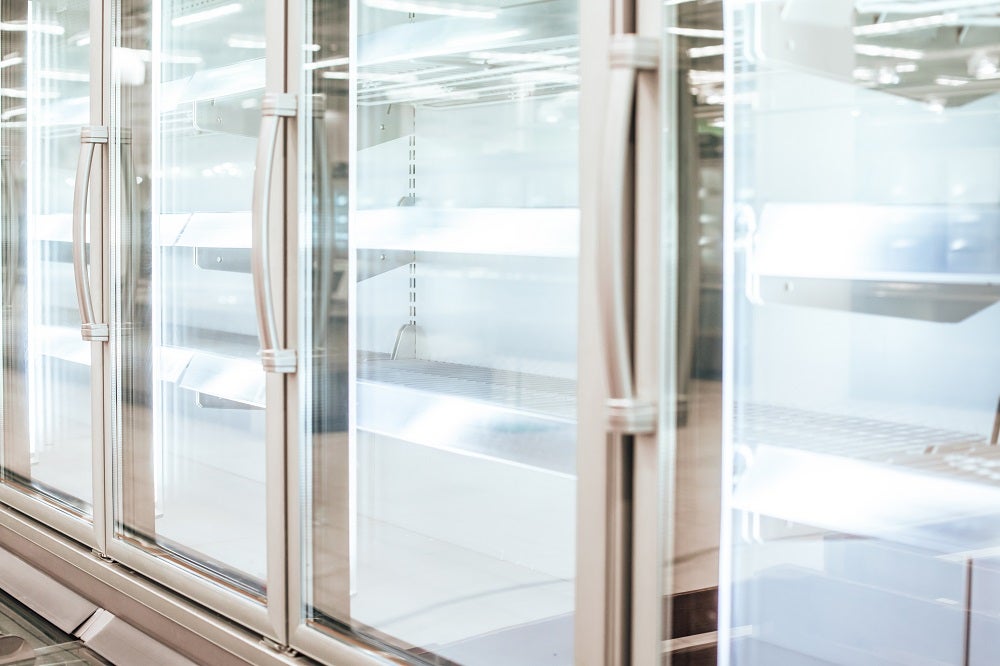
The road to a sustainable future involves some major changes to the way we live and work, but it will also be the small reductions we make in energy consumption that will add up to a major impact on total CO2 emissions.
There are billions of white goods currently operating across the globe, from the domestic machines we use in our homes to large commercial refrigerators, so it stands to reason that choosing energy efficient white goods is not only beneficial to bill payers’ wallets but also for the planet.
EU directive 2017/1369 sets a framework for energy labelling, dictating that an EU Energy Label must be clearly displayed when products such as white goods and bulbs are sold or rented. This was updated in 2021 to introduce a simpler classification that ranks energy efficiency from A to G.
In February, the US Department of Energy (DOE) proposed that energy efficiency standards for refrigerators and washing machines should come into effect by 2027, claiming that new standards could save US consumers approximately $3.5 billion a year on their energy and water bills.
With this in mind, it is becoming imperative for white goods manufacturers to focus on the changes they can make to ensure their product receives a high energy efficiency rating, but where should they start?
Improving sustainability with innovative materials
According to advanced materials expert Alleima, the materials used for each component can have a major impact on the way a final product operates. For example, valves play an essential role in a compressor system, but the characteristics of the steel have a significant effect on the machine’s performance, as well as its energy efficiency.
Through innovative design and using its expertise in metallurgy, Alleima has developed a compressor-valve steel that offers enhanced fatigue properties, which can thrive even in tough operational conditions. This is a critical characteristic for sustainable design as it reduces the amount of energy required by the compressor to perform efficiently.
Freeflex™ from Alleima is a hardened and tempered, martensitic stainless compressor-valve steel that is alloyed with copper. It offers exceptional dimensional tolerance and flatness, extremely high fatigue strength and wear resistance, and has an excellent surface finish. This steel has been used to manufacture flapper valves, reed valves and check valves for applications such as refrigerators, freezers, and air-conditioning equipment.
Exceptional fatigue strength
Freeflex™’s exceptional fatigue strength is achieved in several ways, including improving tensile strength while keeping high ductility by hardening the copper-alloyed steel.
An important factor to note is that Freeflex™ steel’s superior properties enable higher valve lift, which will yield more power with little change to the nature of the power curve.
In addition to helping white goods manufacturers improve the energy efficiency rating of their products, Alleima is committed to decreasing its own impact on the environment. All Alleima strip steel products, including Freeflex™, are therefore manufactured using 82% recycled material and more than 94% fossil-free electricity.
To learn more about the impact of high-quality strip steel on a range of industrial and consumer products, including white goods, download the whitepaper below.