Covid-19 has forced businesses to completely rethink how their supply chains operate. Traditionally, supply networks have been tuned for cost and speed, an approach that relies on having no interruptions. However, as a GlobalData webinar on de-risking supply chains discussed last week, Covid-19 has led to greater importance being placed on resilience.
Rather than suffering supply bottlenecks at single-source suppliers, companies must develop alternative, independent sources. That means having a Plan B and, for critical inputs and sectors, even a Plan C. Having been taken by surprise by Covid-19, companies must also anticipate the steps they would take to counter the threat from any future black swan events, such as a natural disaster, act of war, or even another pandemic.
While coping with the fallout from Covid-19, supply chains have also had to cope with other, man-made challenges, such as political uncertainty and escalating tariff wars between Washington and Beijing.
China’s place in global supply chains is under scrutiny, though the ultimate direction is largely determined by external factors. For example, US clothing retailer Levi’s reduced its production in China because of tariff changes. In 2019, only 1% to 2% of its clothes were made in China, down from 16% in 2017. Coincidentally, its decision to reduce its dependence on Chinese production shielded it from Covid-19 disruption.
Preparing for the unexpected
Preparing for the unexpected is critically important. It means doing scenario planning, running stress tests on every element of supply chains, focusing on delivery from critical suppliers, and doing supply function data analysis. Supply chains typically generate massive amounts of data, and analytics can uncover patterns and offer insights into supply management issues.
One published case study of the cobalt supply chain for an electric vehicle used mapping to highlight the complexity of companies’ supply networks. Critical weaknesses can often lie several tiers deep, possibly among the companies that supply an organisation’s main suppliers.
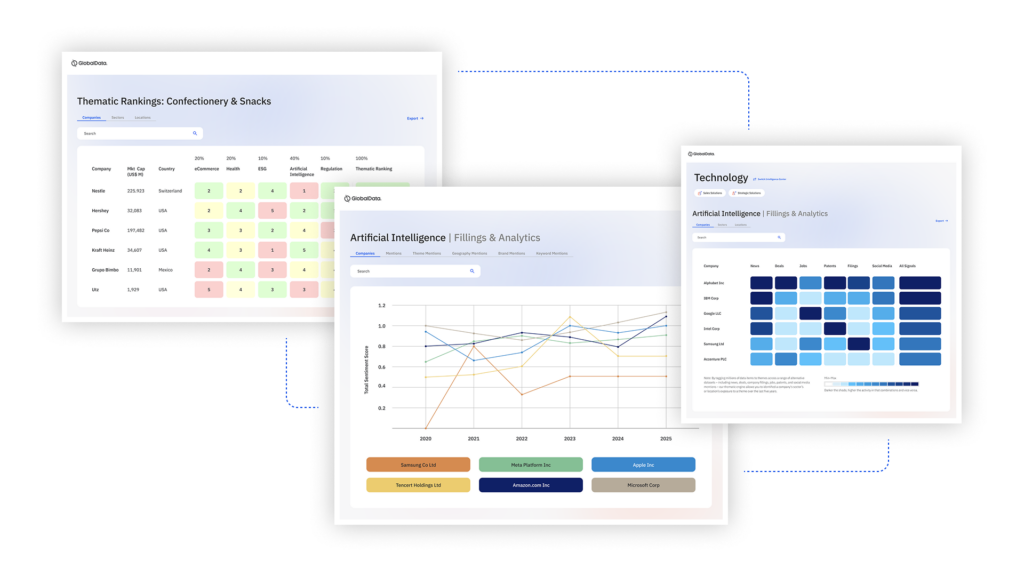
US Tariffs are shifting - will you react or anticipate?
Don’t let policy changes catch you off guard. Stay proactive with real-time data and expert analysis.
By GlobalDataHow Zara shook up its supply chain
One company that has already rethought its supply chain in the face of Covid-19 is clothing supplier Zara. Zara’s super-fast fashion innovation relies on agility and, consequently, it has reconfigured its conventional supply chain. Zara makes 12 inventory turns a year; its competitors typically have three or four. As a result, Zara is more flexible and needs less inventory finance. It also has a dual response strategy in that basic styles are made in different countries of the world whenever demand is unpredictable.
Supply in an uncertain world
In their response to the pandemic, companies in most sectors must examine how their supply chains have performed and decide how, and at what pace, they want to shake them up.
In an increasingly turbulent world, deciding how exposed a company is to its supplier network, and what to do about it, will become a critical theme for companies. No chief executive will want to be kept awake at night worrying about their supply-chain.